
Large industrial pipes are joined together by flanges.Ī pipe “flange” is a ring of metal, usually welded to the end of a pipe, which is compressed against the shoulder of the matching female fitting. Like the SAE parallel-thread standard, sealing is accomplished by means of an O-ring Like the BSPT (tapered) standard, the thread angle of BSPP is 55 o. The threads serve only to provide force (not fluid sealing).Īnother parallel-thread pipe standard is the BSPP, or British Standard Pipe Parallel.

Sealing is accomplished as the O-ring is compressed against the shoulder of the female fitting. Is the SAE straight thread, after the Society of Automotive Engineers In the United States, a common design of parallel-thread pipe fitting On stainless steel a double wrap is recommended to minimizeĪny possible galling, while providing a good seal.Īn alternative to tapered threads in pipe joints is the parallel thread.
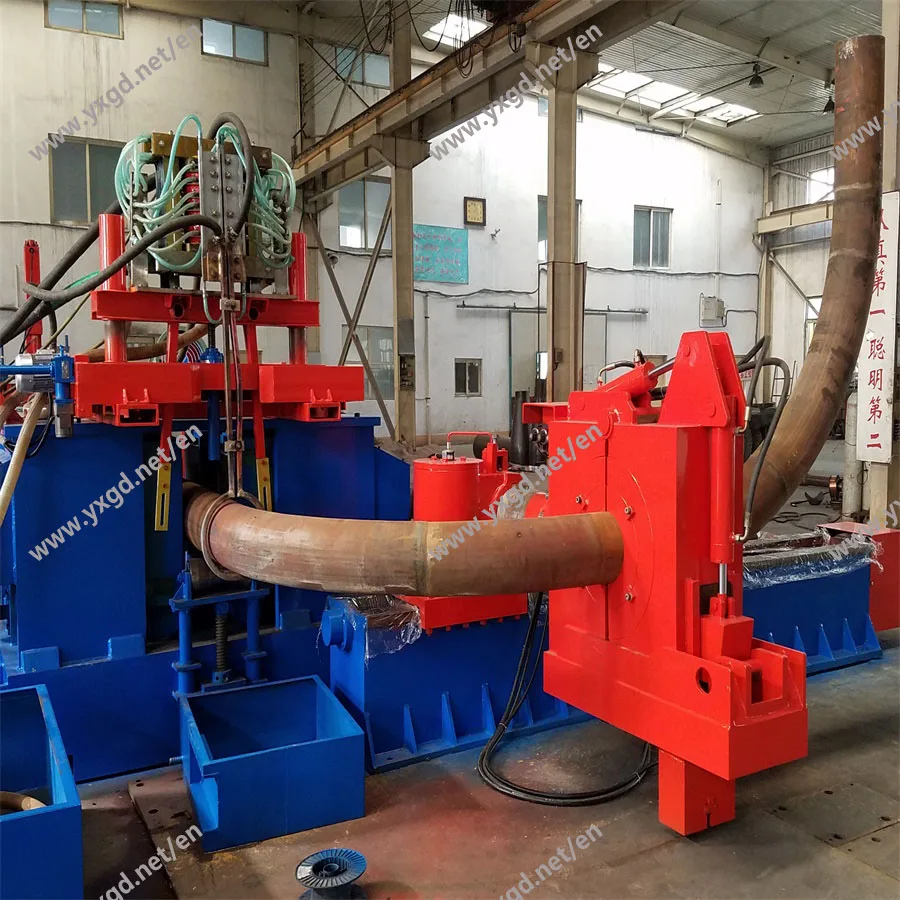
Wrap of the tape, (1¼ turns is recommended)overlapping slightly.īe sure the tape does not overhang the first thread otherwise the tape couldĭeteriorate and contaminate the fluid system. Wrap the tape in the direction (clockwise) of the thread.ĭraw the tape tightly around the thread, ensuring, at a minimum, one complete Of mating taper threads in order to prevent formation of a spiral leak path. Preventing galling, and filling the gap between the crests and roots Thread tape acts as a lubricant allowing more thread engagement,
#Instrument tube bending free
NPT fittings must be made leak free with the aid of thread seal tape or standard for tapered threads used to join pipes and fittings. The taper on NPT threads allows them to form a seal when torqued as the flanks of the threads compress against each other. The intent of a tapered thread is to allow the pipe and fitting to “wedge” together when engaged, creating a joint that is both mechanically rugged and leak-free. When male and female tapered pie threads are first engaged, they form a loose junction: This eliminates thrust in all directions.įor smaller pipe sizes, threaded fittings are more commonly used to create connections between pipes and between pipes and equipment (including some instruments). When tubing is left unsupported, shock and vibration will cause the tubing to shake, and in turn, cause the fitting to loosen and leak or even allow tube to fail through fatigue. Tubing can be clamped individually, in sets, and can also be stacked.īelow you will find a chart of recommended spacing between clamps.Ĭlamp as close to each bend of the tube as possible and you must clamp each side. Vertical ganging additionally increases system safety, since, for example, floor-level horizontally ganged tubing may be stepped on. Vertical ganging prevents the collection of dirt or any potentially corrosive medium. To the maximum extent possible, tubing should be ganged vertically rather than horizontally. When offsetting in a ganged run, stagger the union locations to further ensure ease of access. Offset bends are used to increase accessibility to tube fitting unions for maintenance purposes. Have a neat appearance and allow for easy trouble shooting, maintenance and repair. Keep tube lines away from components that require regular maintenance. U-Bend Allowing for Expansion and Contraction Routing of lines is probably the most difficult yet most significant of these system design considerations. Proper routing involves connecting one point to another through the most logical path.Īvoid excessive strain on joints - A strained joint will eventually leak.Īllow for expansion and contraction - Use a “U” bend to allow for expansion and contraction. Tees may have one pipe end and two tube ends (branch tees and run tees), or three tube ends (union tees).The only difference between a branch tee and a run tee is the orientation of the pipe end with regard to the two tube ends Tee fittings join three fluid lines together.
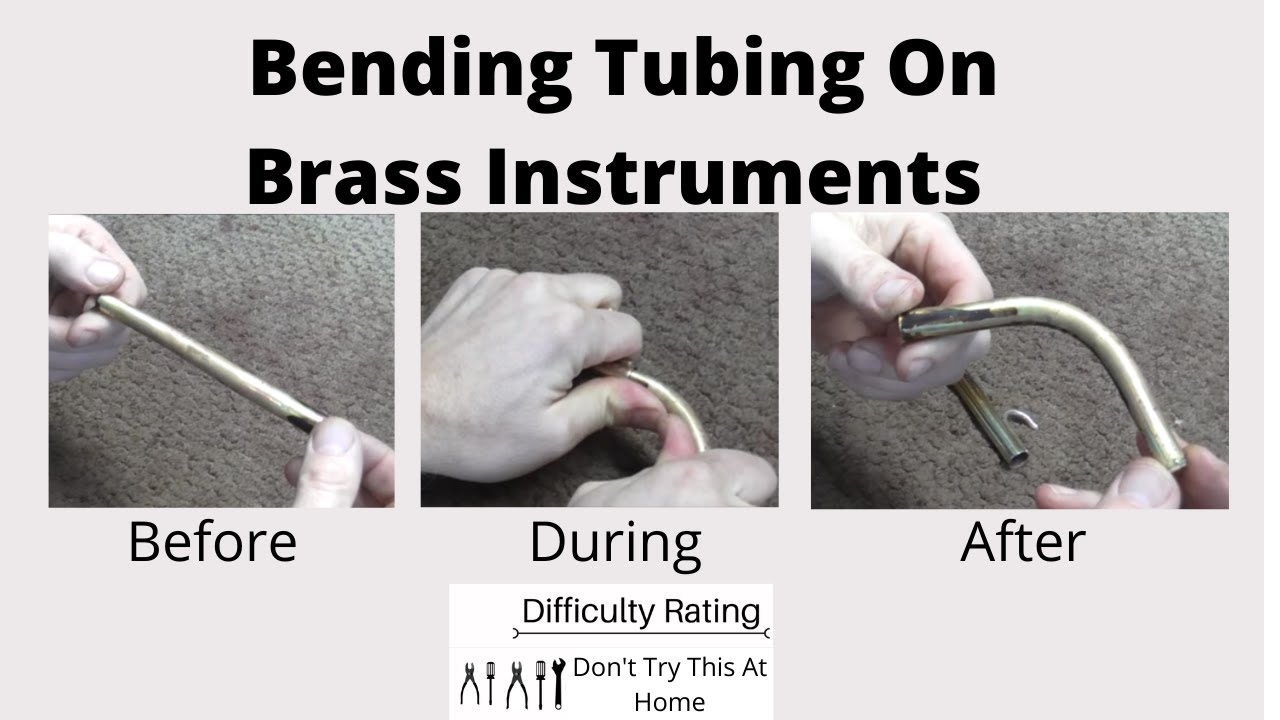
Like standard connectors, they may terminate in male pipe thread, female pipe threads, or in another tube end. These are useful for making turns in tube runs without having to bend the tubing itself. Tubing elbows are tube connectors with a bend. If a tube union joins together different tube sizes rather than tubesīulkhead fittings are designed to fit through holes drilled in panels or enclosures to provideĪ way for a fluid line to pass through the wall of the panel or enclosure.
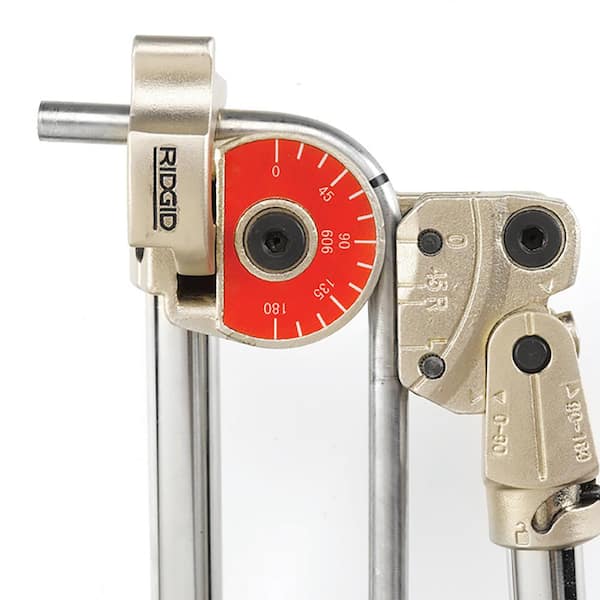
burrs can restrict flow, as well as possibly break loose and damage fine filtration elements.īurrs forms after using Tube Cutter Deburring Tool burrs can prevent tubing from seating properly in a fitting body. The burrs formed by either the tube cutter or hacksaw must be removed prior to assembly to prevent those burrs from eventually damaging the system.
